Legal updates
Government amendments to the Employment Rights Bill – key takeaways for employers
10 July 2025
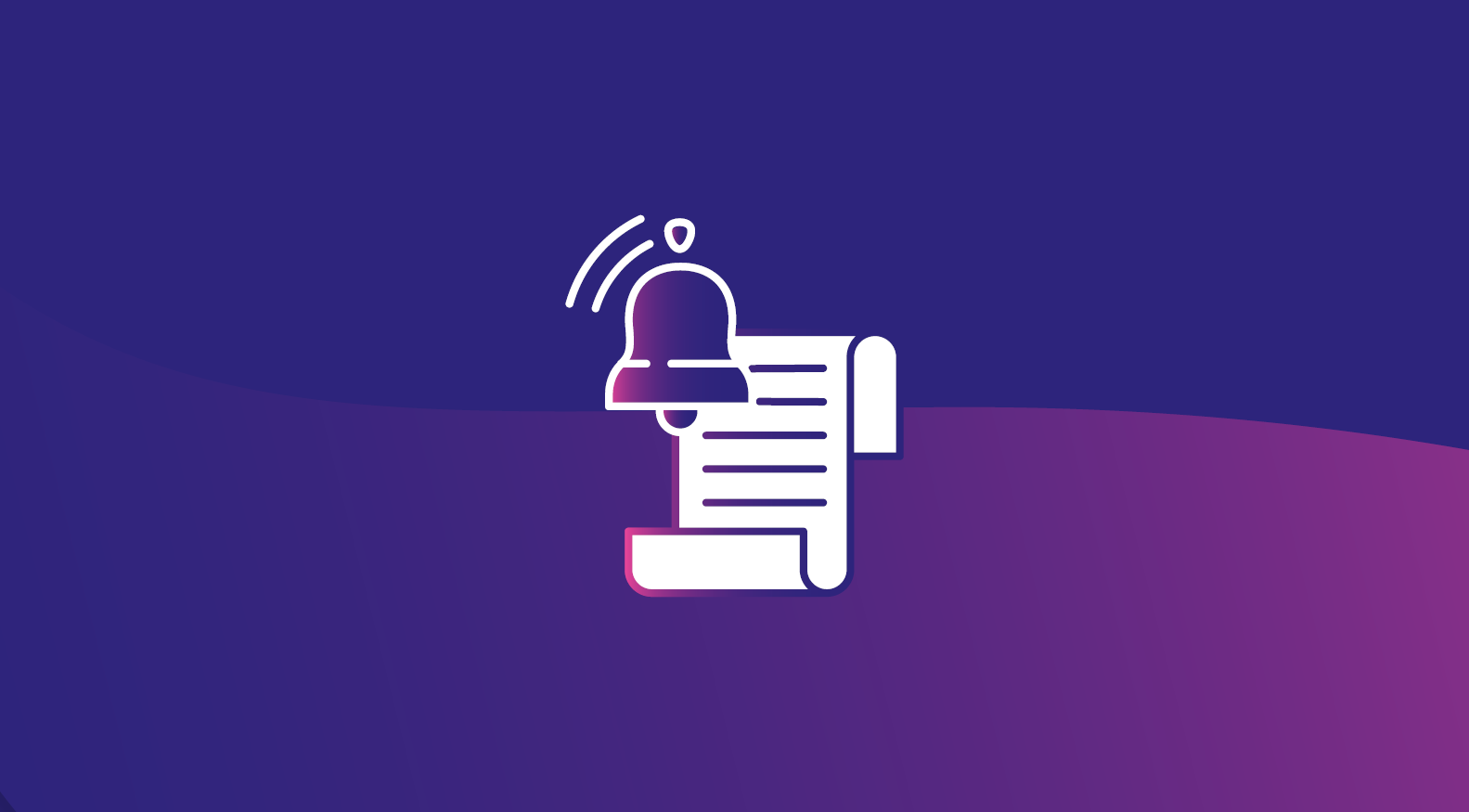
This website will offer limited functionality in this browser. We only support the recent versions of major browsers like Chrome, Firefox, Safari, and Edge.
Legal updates
10 Jul 2025
Thought leadership
10 Jul 2025
See what’s coming up, register for the events that matters to you and discover our range of on-demand content.
See upcoming eventsEssential listening for you and your organisation.
Discover our range of podcast series and subscribe to make sure you don’t miss an episode.
Listen now